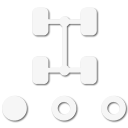
Off-Road Ranger I
With the primary electrics done I can move on to the plumbing work.
The upper coolant connection was straight forward thanks to the modifications to the radiator's inlet port, just a simple 45-degree 1.75" layered silicone hose with stainless t-bolt clamps that I'm using throughout:
These "U" and "J" bends make fabrication easy, even without a bender, & with very smooth transitions thanks to the mandrel bending machine that makes them. I would like to use stainless steel tubing, but until I get my own TIG welder I'll use this heavy gauge steel exhaust pipe that I can easily MIG weld:
The lower coolant pipe I made is a 45-degree elbow with a short leg on 1 side to join the 2 hoses, with beads formed using the modified vise-grip:
The engine's new coolant inlet connection uses a short 2" diameter hose, then the new elbow, & down to the radiator with a 90-degree elbow hose:
Before I moved onto the charge piping I needed to do some welding experiments with different weld puddle techniques, tubing gauge, plated vs raw steel, gap vs flush, & taper angle in the joints between them (plus a not so subtle joke for a friend). Best welds I made were with .024" wire, a fast u-shape drag, 14 gauge unplated tube, 30-degree joint taper, & little to no gap:
Plenty of figuring & marking to keep me from messing up as I started with the hot-side charge piping, all in 2.5" diameter. Glad I got a bunch of practice building a header & full exhaust system for another project before digging into this more detailed build:
My hot-side pipe turned out as smooth & short as I could've hoped for. From a v-banded aluminum elbow off the Super HX30, to a silicone hump hose, then the new pipe, & into the Freightliner charge cooler with a reinforced silicone coupler:
The cold-side charge pipe wasn't much more complicated on the other side of the engine, with pair of 90-degree bends linked together & the same compliment of hoses:
Grinding the welds back wasn't necessary, more for fun than anything... at least until I learn TIG that's more well suited for this kind of work:
Next up I'll build a turbo dump pipe as paint dries on the new pipes, then it's on to fluid fill ups!
The upper coolant connection was straight forward thanks to the modifications to the radiator's inlet port, just a simple 45-degree 1.75" layered silicone hose with stainless t-bolt clamps that I'm using throughout:
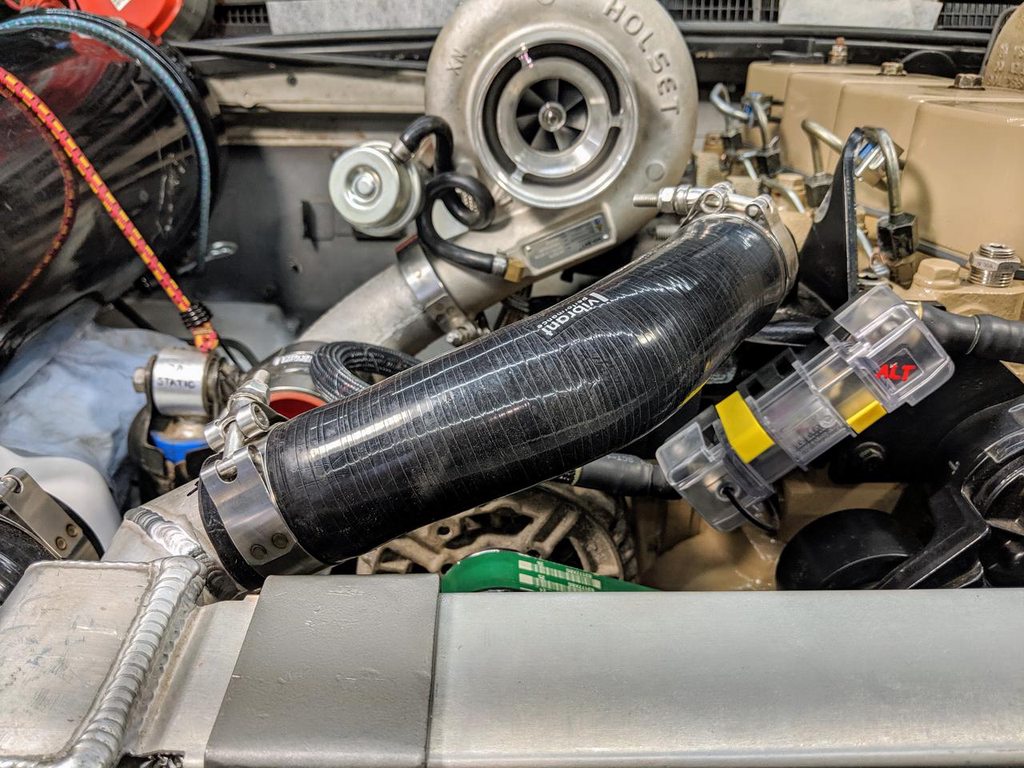
These "U" and "J" bends make fabrication easy, even without a bender, & with very smooth transitions thanks to the mandrel bending machine that makes them. I would like to use stainless steel tubing, but until I get my own TIG welder I'll use this heavy gauge steel exhaust pipe that I can easily MIG weld:
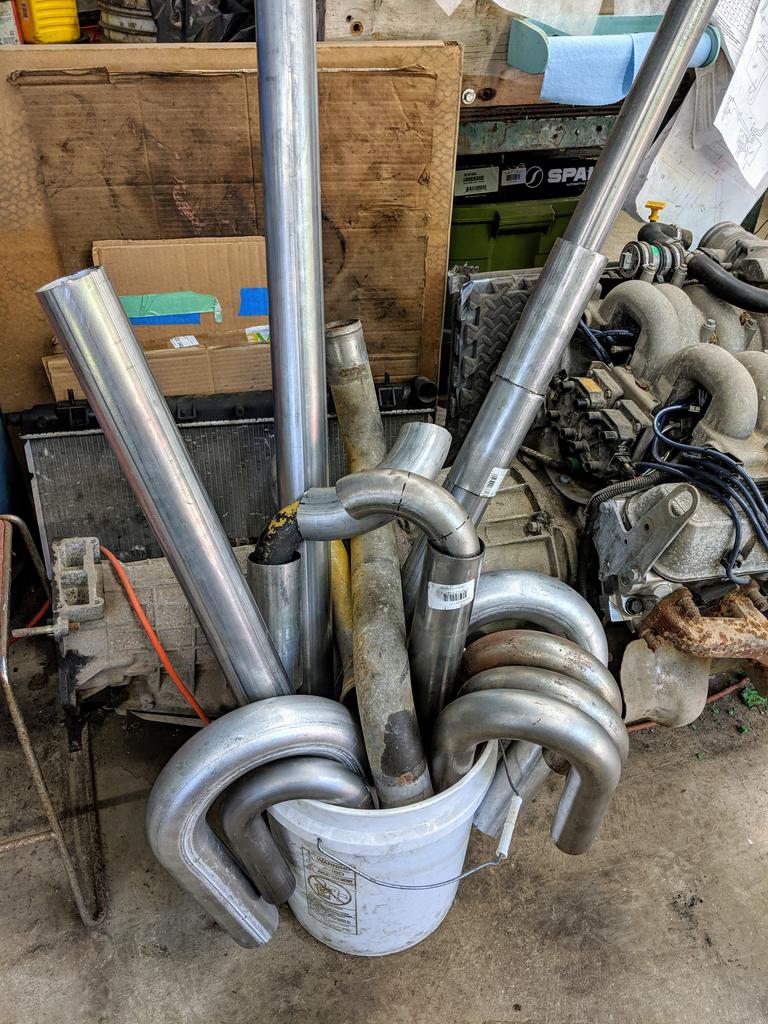
The lower coolant pipe I made is a 45-degree elbow with a short leg on 1 side to join the 2 hoses, with beads formed using the modified vise-grip:
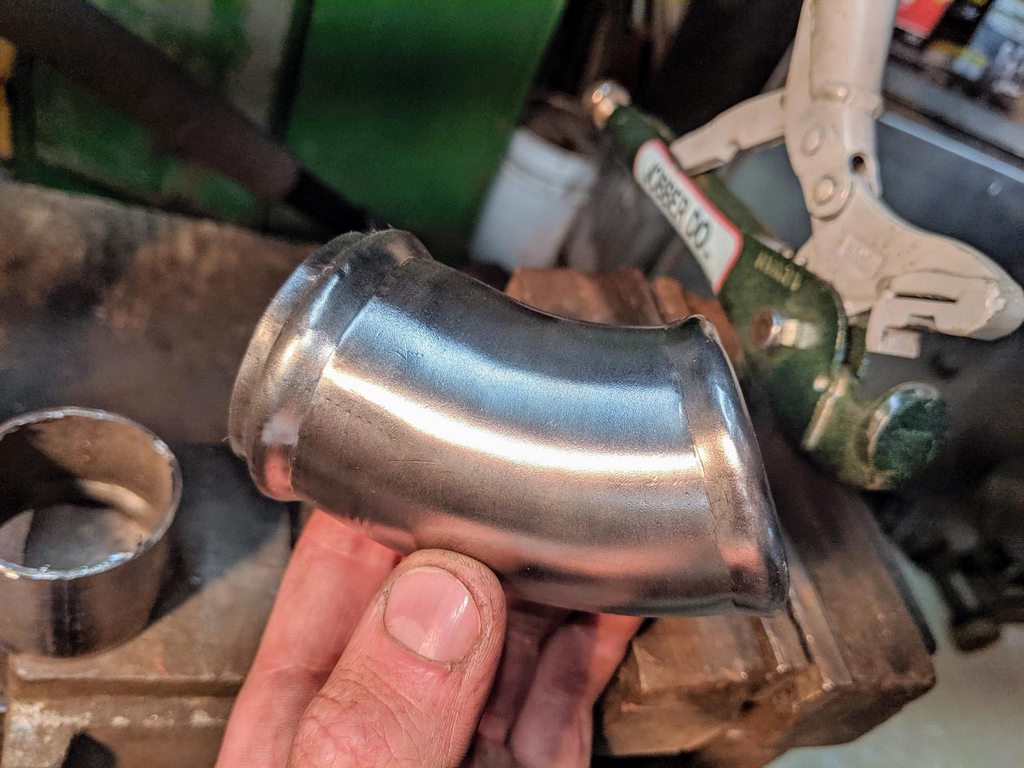
The engine's new coolant inlet connection uses a short 2" diameter hose, then the new elbow, & down to the radiator with a 90-degree elbow hose:
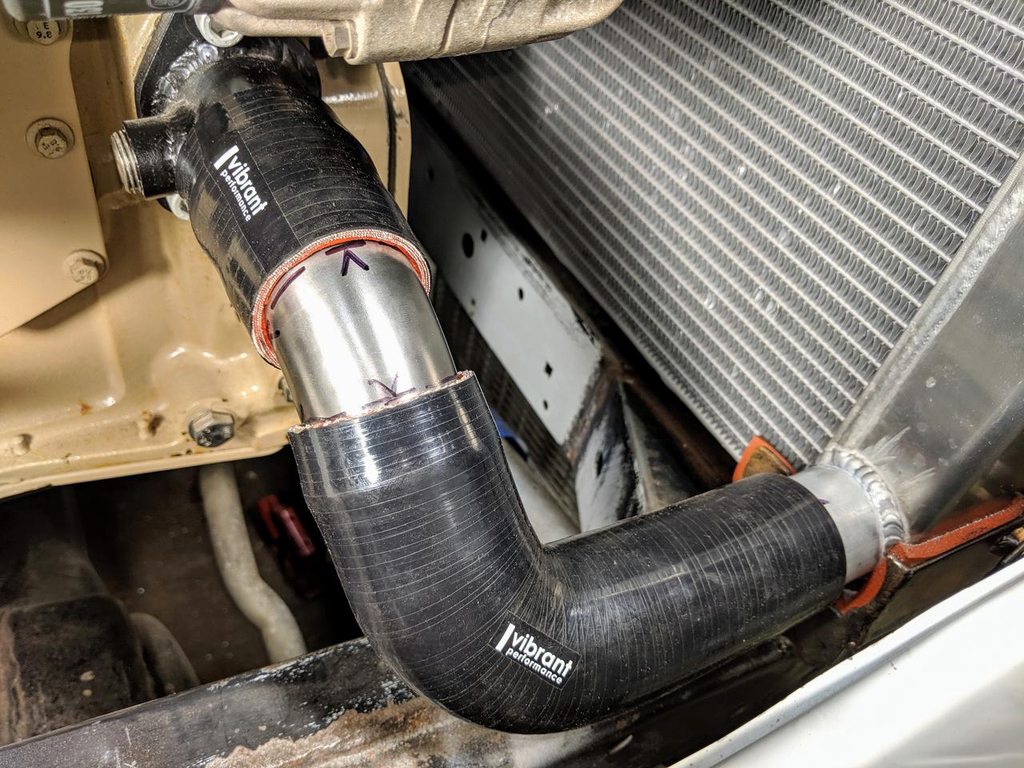
Before I moved onto the charge piping I needed to do some welding experiments with different weld puddle techniques, tubing gauge, plated vs raw steel, gap vs flush, & taper angle in the joints between them (plus a not so subtle joke for a friend). Best welds I made were with .024" wire, a fast u-shape drag, 14 gauge unplated tube, 30-degree joint taper, & little to no gap:
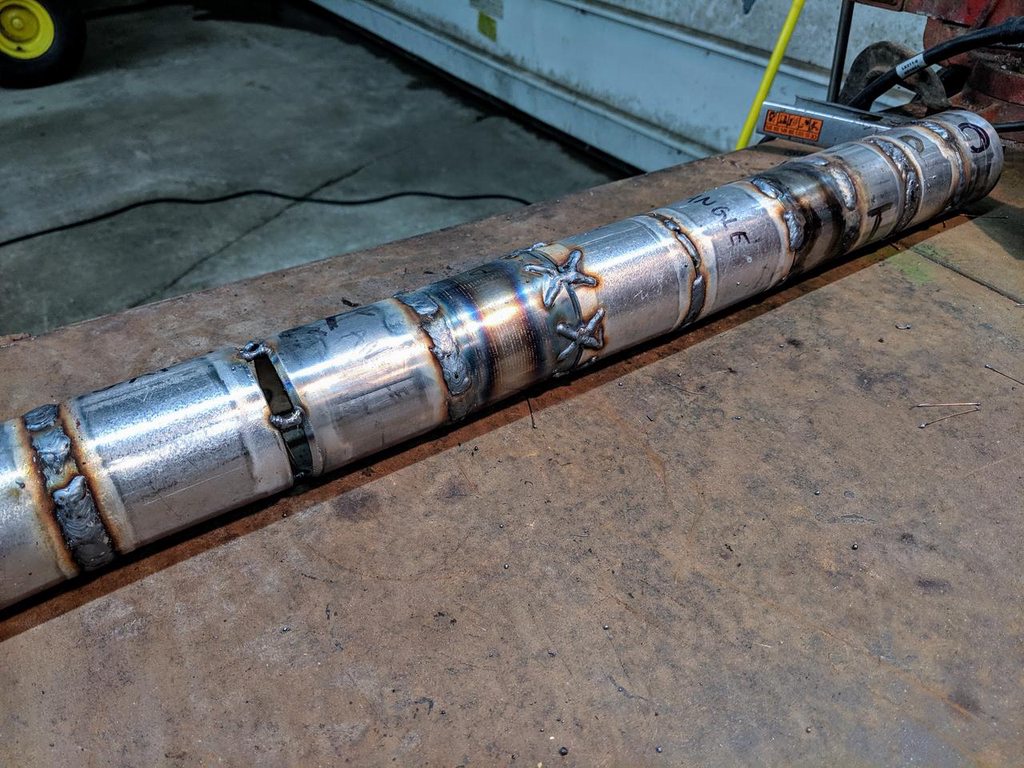
Plenty of figuring & marking to keep me from messing up as I started with the hot-side charge piping, all in 2.5" diameter. Glad I got a bunch of practice building a header & full exhaust system for another project before digging into this more detailed build:

My hot-side pipe turned out as smooth & short as I could've hoped for. From a v-banded aluminum elbow off the Super HX30, to a silicone hump hose, then the new pipe, & into the Freightliner charge cooler with a reinforced silicone coupler:
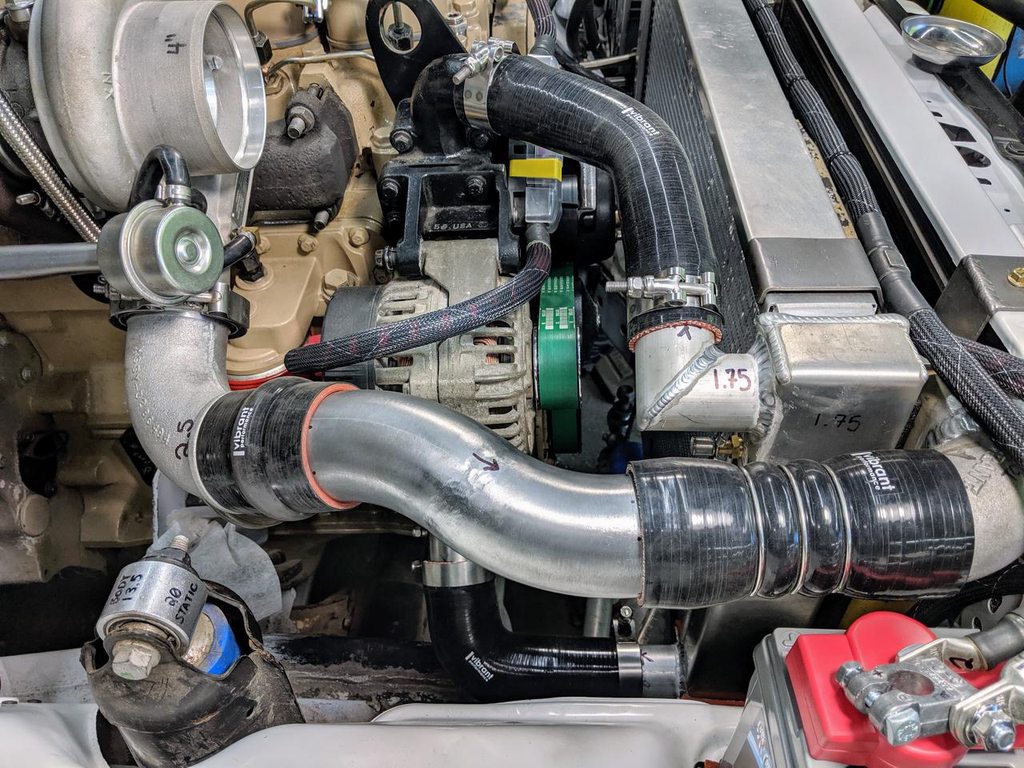
The cold-side charge pipe wasn't much more complicated on the other side of the engine, with pair of 90-degree bends linked together & the same compliment of hoses:
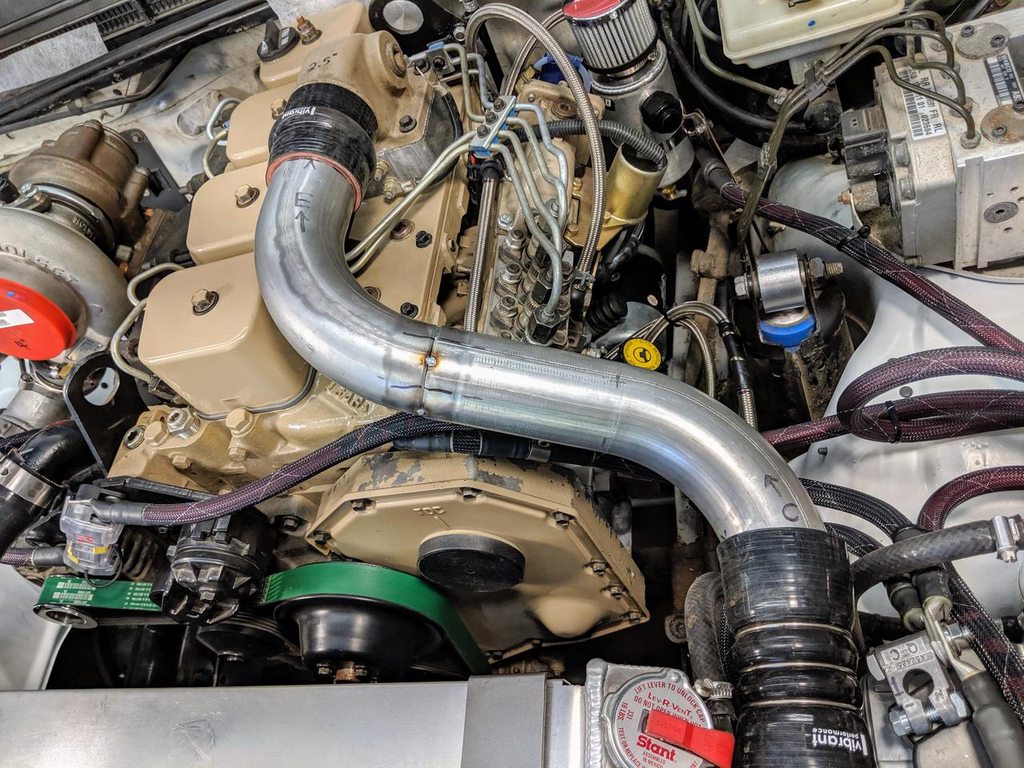
Grinding the welds back wasn't necessary, more for fun than anything... at least until I learn TIG that's more well suited for this kind of work:
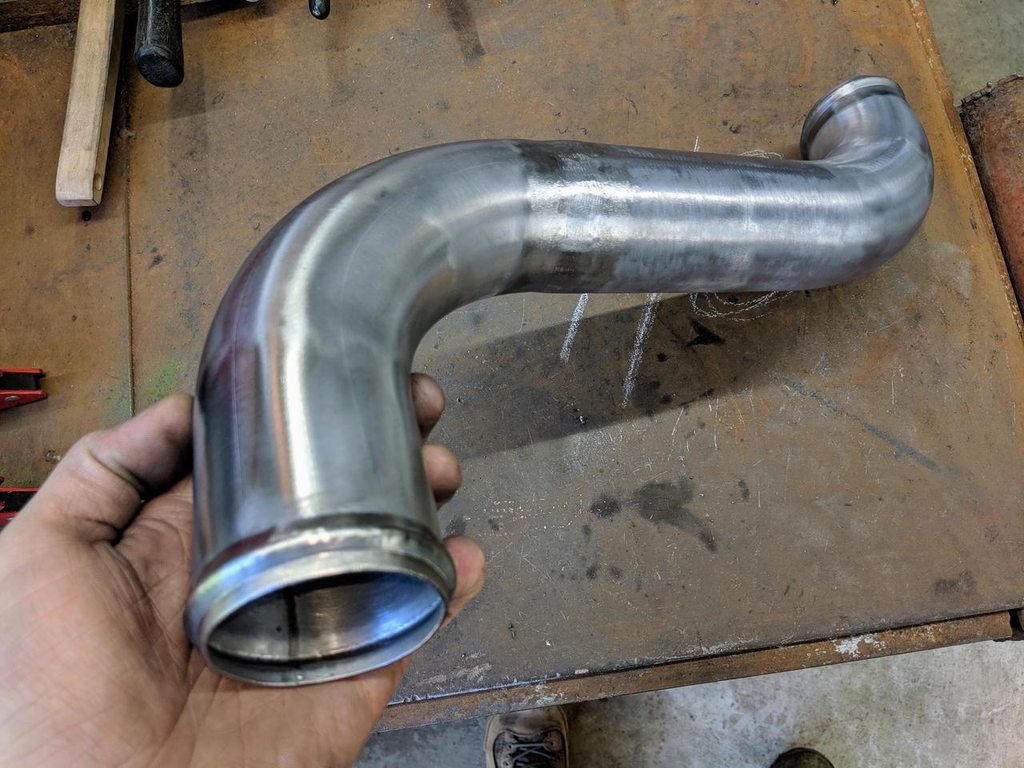
Next up I'll build a turbo dump pipe as paint dries on the new pipes, then it's on to fluid fill ups!