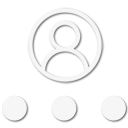
Member III
- 2,827
- First Name
- Tom
- Last Name
- Houston
- Member #
-
8300
- Ham/GMRS Callsign
- WØNUT Extra
"Welcome to my build thread". My purpose was to design from scratch and build an offroad “teardrop” trailer.
While technically, the shape is not a pure teardrop, the same purpose is the goal. This was built as a prototype for a possible product.
My design goals were to be able to pull it on severe off road trails behind my 1985 Jeep Cherokee XJ. I’ve had it for over 22 years and it is extremely capable but I got tired of sleeping in the back of my rig and that really doesn’t work for my “city girl” wife.
The Jeep is on 35’s and the hitch sits pretty high so the tongue will be non-traditional. The trails I take are really rough and require a lot of twist and rotation as well as being able to take a pounding without beating up the contents.
Here is the final result.
My suspension design utilizes a dual air bag suspension with shocks using 31" tires.
Unlike most builders, I didn’t start with a trailer. I started with a pile of steel on the floor.
While technically, the shape is not a pure teardrop, the same purpose is the goal. This was built as a prototype for a possible product.
My design goals were to be able to pull it on severe off road trails behind my 1985 Jeep Cherokee XJ. I’ve had it for over 22 years and it is extremely capable but I got tired of sleeping in the back of my rig and that really doesn’t work for my “city girl” wife.
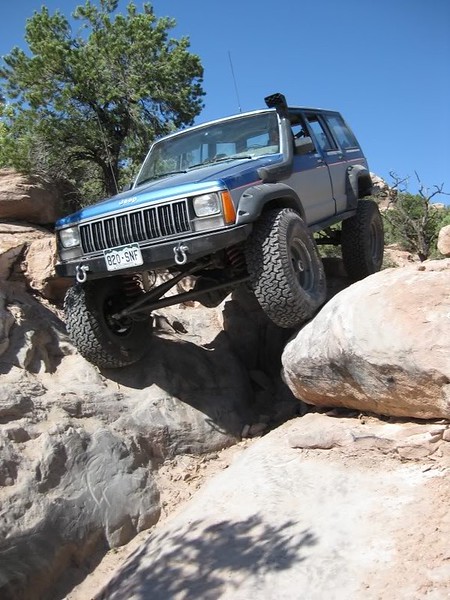
The Jeep is on 35’s and the hitch sits pretty high so the tongue will be non-traditional. The trails I take are really rough and require a lot of twist and rotation as well as being able to take a pounding without beating up the contents.
Here is the final result.
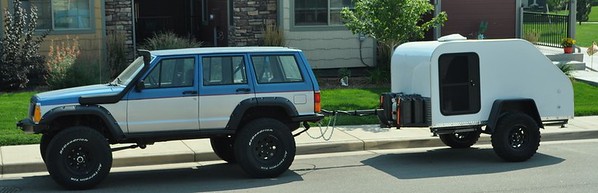
My suspension design utilizes a dual air bag suspension with shocks using 31" tires.
Unlike most builders, I didn’t start with a trailer. I started with a pile of steel on the floor.
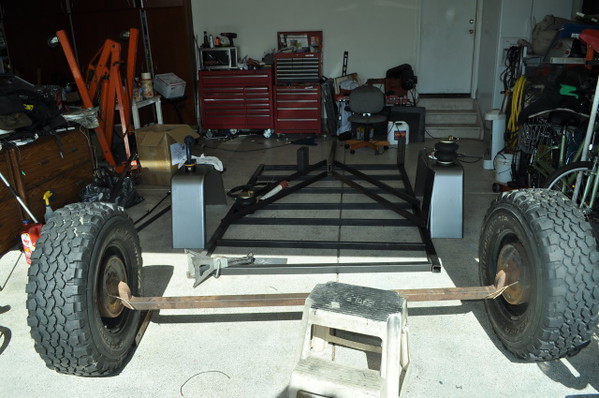