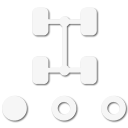
Off-Road Ranger I
From time to time 4WD’s will need to be recovered from various situations where the vehicle’s capabilities have been exceeded. There are several reasons why vehicles may become immobilised:
1.Poor appreciation or investigation of the route involved, due to:-- Lack of knowledge of the area, or Poor appraisal of the terrain.
2.Driving without due care and attention.
3.Stopping or stalling on poor surfaces.
4.Mechanical break-down.
5.Lost traction or momentum
Recovery Points
All vehicles are fitted with towing/tie down points from the factory. They are designed to do what the name suggests – tie the vehicle down during transport or shipping.They must never be used for recovery.
Your point of attachment to the vehicle must be rated for its purpose and inspected prior to using it.
Towing or tie down points Most vehicles are fitted with factory tow points. These are generally made of
a heavier material such as a loop of steel rod and attached to the chassis by bolts or more commonly welded. These are designed to tow the car with however they are not suitable for recovery due to the shock loadings that occur.
This is a typical towing/tie down point that has been used for recovery.
View attachment 1574
You can see in the image that the area that is welded to the chassis has torn and is therefore compromised. This was an accident waiting to happen
Rated recovery points
Many people believe that just because you purchase a rated recovery point and bolt it to your vehicle that it is fine to recover off. This is not always the case. These items are all rated in their own right however consideration needs to be exercised when these are on the vehicle. Some bolt up directly to factory
holes and others require the chassis to be drilled. Where they bolt to factory holes generally these points on the chassis are reinforced and will take the load better than other sections of the chassis.These items should always be installed by either the point of purchase or through your authorised service agent for your vehicles.
All recovery points must be inspected before each use to ensure that they have no visible signs of damage. In the case of recovery hooks, they must also have an intact keeper that prevents your attached recovery system from falling off
View attachment 1575
Never use a trailer hitch tow ball as an attachment point during recoveries
A trailer hitch tow ball is not designed or rated to be used during recoveries.However the hitch pin is more than capable for the task by using a sling to secure it to. Alternatively there are a range of products available that can be fitted into the receiver to provide a rated recovery attachment point as in this example
View attachment 1576
Operation of Winch's
Make yourself familiar with the type of winch that you possess. Whenever handling a winch steel wire rope (SWR) gloves must always be worn to avoid injury to hands from damaged or frayed wire. Take the time to un-roll the electric winch SWR and pace out its length. When pacing the length of the winch SWR it also provides the opportunity to inspect it. This should be done before the winch is ever used. Attention to this
can assist you later when trying to find the optimum distance from your anchor point, without falling short. Never use the SWR for towing as it can damage both the winch and the SWR. After using the SWR, feed it back on to the winch drum. It should feed neatly and evenly as it runs along the winch drum and then back the other way. Endeavour to pull it in a straight line. The winch has been designed to cope with a slight angled pull, but its strength is severely reduced when the SWR is deployed around corners on the fairlead, or the hook up eye at the SWR's end.
Safety when winching
Whenever any recovery is made by winching you should adopts the following safety procedure:-
The operator of the winch hand control is to be seated in the driver’s position and able to steer the vehicle as needed. Make sure an inertia dampener like a blanket is laid over the centre of the SWR. This will work as a shock absorber, removing a large percentage of the stored energy in the taut SWR as it breaks; resulting in the broken ends dropping to the ground and ceasing motion in a shorter distance.
Steel wire rope makes a singing sound just before it breaks.‘Sing and run’
When using the electric winch, take up the slack by ‘pulsing’ the power button.This prevents the slack SWR or shear pin from breaking because of a sudden momentary ‘shock load’ which can exceed the rating of either component.
Enough slack is taken up to the point where the SWR is placed under tension from the intended load.
Recheck connections before proceeding.When the hook is about a metre from the fairlead, use the pulsing method again to pull in the remainder of the SWR. Keep fingers and hands well clear.Increase the engine speed on the vehicle whilst its winch is being operated.This enables the vehicle to maintain charge in its electrical system. Only use the winch in short bursts to avoid overheating the winch motor. During any
pauses in the process, carefully monitor the connections. If possible chock the vehicle’s wheels to reduce the strain on the winching system
All bystanders must be a minimum distance of 1.5 times the length of the payed out winch SWR from any point within the danger zone radius.Never step over a connected winch rope. Always go around the vehicle oranchor point to get to the other side.
Synthetic winch rope
The rope that is fitted to a vehicles winch introduces a number of hazards to the operator and thankfully SWR is not the only choice available. There are a variety of synthetic rope options that can be fitted to most winches now that are lighter, more flexible and have less associated risks.Consult with a reputable dealer if you intend to replace an older damaged SWR on your vehicles winch, as the roller fairlead must also be replaced when this change is made. There is also an issue with heat in some older winches that prevents this replacement from being possible.The same winching process is used no matter which rope type is fitted
1.Poor appreciation or investigation of the route involved, due to:-- Lack of knowledge of the area, or Poor appraisal of the terrain.
2.Driving without due care and attention.
3.Stopping or stalling on poor surfaces.
4.Mechanical break-down.
5.Lost traction or momentum
Recovery Points
All vehicles are fitted with towing/tie down points from the factory. They are designed to do what the name suggests – tie the vehicle down during transport or shipping.They must never be used for recovery.
Your point of attachment to the vehicle must be rated for its purpose and inspected prior to using it.
Towing or tie down points Most vehicles are fitted with factory tow points. These are generally made of
a heavier material such as a loop of steel rod and attached to the chassis by bolts or more commonly welded. These are designed to tow the car with however they are not suitable for recovery due to the shock loadings that occur.
This is a typical towing/tie down point that has been used for recovery.
View attachment 1574
You can see in the image that the area that is welded to the chassis has torn and is therefore compromised. This was an accident waiting to happen
Rated recovery points
Many people believe that just because you purchase a rated recovery point and bolt it to your vehicle that it is fine to recover off. This is not always the case. These items are all rated in their own right however consideration needs to be exercised when these are on the vehicle. Some bolt up directly to factory
holes and others require the chassis to be drilled. Where they bolt to factory holes generally these points on the chassis are reinforced and will take the load better than other sections of the chassis.These items should always be installed by either the point of purchase or through your authorised service agent for your vehicles.
All recovery points must be inspected before each use to ensure that they have no visible signs of damage. In the case of recovery hooks, they must also have an intact keeper that prevents your attached recovery system from falling off
View attachment 1575
Never use a trailer hitch tow ball as an attachment point during recoveries
A trailer hitch tow ball is not designed or rated to be used during recoveries.However the hitch pin is more than capable for the task by using a sling to secure it to. Alternatively there are a range of products available that can be fitted into the receiver to provide a rated recovery attachment point as in this example
View attachment 1576
Operation of Winch's
Make yourself familiar with the type of winch that you possess. Whenever handling a winch steel wire rope (SWR) gloves must always be worn to avoid injury to hands from damaged or frayed wire. Take the time to un-roll the electric winch SWR and pace out its length. When pacing the length of the winch SWR it also provides the opportunity to inspect it. This should be done before the winch is ever used. Attention to this
can assist you later when trying to find the optimum distance from your anchor point, without falling short. Never use the SWR for towing as it can damage both the winch and the SWR. After using the SWR, feed it back on to the winch drum. It should feed neatly and evenly as it runs along the winch drum and then back the other way. Endeavour to pull it in a straight line. The winch has been designed to cope with a slight angled pull, but its strength is severely reduced when the SWR is deployed around corners on the fairlead, or the hook up eye at the SWR's end.
Safety when winching
Whenever any recovery is made by winching you should adopts the following safety procedure:-
The operator of the winch hand control is to be seated in the driver’s position and able to steer the vehicle as needed. Make sure an inertia dampener like a blanket is laid over the centre of the SWR. This will work as a shock absorber, removing a large percentage of the stored energy in the taut SWR as it breaks; resulting in the broken ends dropping to the ground and ceasing motion in a shorter distance.
Steel wire rope makes a singing sound just before it breaks.‘Sing and run’
When using the electric winch, take up the slack by ‘pulsing’ the power button.This prevents the slack SWR or shear pin from breaking because of a sudden momentary ‘shock load’ which can exceed the rating of either component.
Enough slack is taken up to the point where the SWR is placed under tension from the intended load.
Recheck connections before proceeding.When the hook is about a metre from the fairlead, use the pulsing method again to pull in the remainder of the SWR. Keep fingers and hands well clear.Increase the engine speed on the vehicle whilst its winch is being operated.This enables the vehicle to maintain charge in its electrical system. Only use the winch in short bursts to avoid overheating the winch motor. During any
pauses in the process, carefully monitor the connections. If possible chock the vehicle’s wheels to reduce the strain on the winching system
All bystanders must be a minimum distance of 1.5 times the length of the payed out winch SWR from any point within the danger zone radius.Never step over a connected winch rope. Always go around the vehicle oranchor point to get to the other side.
Synthetic winch rope
The rope that is fitted to a vehicles winch introduces a number of hazards to the operator and thankfully SWR is not the only choice available. There are a variety of synthetic rope options that can be fitted to most winches now that are lighter, more flexible and have less associated risks.Consult with a reputable dealer if you intend to replace an older damaged SWR on your vehicles winch, as the roller fairlead must also be replaced when this change is made. There is also an issue with heat in some older winches that prevents this replacement from being possible.The same winching process is used no matter which rope type is fitted