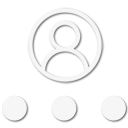
Member III
This is a cut and paste job of a build thread I posted on a few other forums. It may seem a bit out of context in places timing wise. I had a couple of major diversions (all good) that delayed my build but I have made a lot of progress on the trailer since my last post in that thread. I will update this thread as soon as I can. The trailer is "almost" completed!
A few years ago I started to make some rough sketches of what I wanted to build as an expedition style trailer. I built a utility trailer 3 or 4 years ago. It was a fun project and I wanted to build another one.
I bought some metal for the frame and started to cut it to size. I was literally about to start welding when I found a trailer for sale on a local Jeep forum. It was very close to what I planned to build and the price was more than right. I couldn't have bought the materials for what I paid for the trailer.
It was only a little more than an hour away. I drove down thinking I would have to repack the bearings, reconstruct the coupler, etc. but it was in perfect condition. I drove it away and was fully confident with it within 10 miles or so. Thanks Just-lift; good deal!
The overall specs are;
- length 12'
- width 5' 10";
- height 3' 5" (without lid)
- clearance 19.75" to frame
- clearance 15" to axle
- tongue platform tapering to 32"
- weight not sure yet !!!
- axle 3,500 lb. (brakes to come)
- wheels 16" Jeep Moab
- tires 245 75R 16 Goodyear Duratrac
- box length 5'
- box width 4'
- box height 19.25"
- box cubic ft. 32 ft(3)
- tongue jack 1,500 lbs.
Here's what I started with. This pic from the ad for it was either taken on the day it was painted or it was more likely raining. It looked shinier that it was.
The trailer was well constructed. I understand it was used by a welding company to trailer a mobile welder to job sites. The round fenders were well built and nicely tied to the frame with deck plate running boards. It had 14" wheels and tires that were in pretty good shape. I wanted square fenders though and 16" wheels and tires to match my Jeep TJ & XJ so I decided to tear everything off.
I sanded down a pair of 16" Jeep Moab wheels and painted them with Duplicolor wheel paint. I'll eventually get them powder coated. I went with graphite to distinguish them from the silver wheels on the tow vehicles. I found an almost new set of 245/75R/16 Goodyear Duratracs on Kijiji to match what I have on my TJ. I also needed a set of spacers to mount the wheels to the hubs. I may replace the axle so I can add brakes. Unlike a lot of axles the current one does not have the flanges to bolt the brake backing plates to. If I can fabricate something suitable I'll go that route. If not I'll build a new axle.
I cut off the trailer jack that came with the trailer and welded on brackets to attach a 1,500 lb. marine jack. I like the wheel/tire and hope it handles dirt surfaces better than the more common narrow tires.
The trailer bed was pretty rusty and had about 30 bolt, rivet and rust holes that needed to be filled.
Scraps from the old running boards came in handy.
The chassis was built by a company called EZ Tow Trailers. I like the curved side rails which is something I didn't plan for in my original sketches.
I spent a lot of time underneath it getting rid of the rust.
I eventually flipped it over and that seemed like the right time to add a receiver to the rear bumper for a bike rack, etc.
With a lot of the rust gone I painted the frame with POR15 and later with a few different types of cheap aerosol bed liners. I thought I'd try a different ones out and recoat everything with the one I finally like (no decision yet).
A few years ago I started to make some rough sketches of what I wanted to build as an expedition style trailer. I built a utility trailer 3 or 4 years ago. It was a fun project and I wanted to build another one.
I bought some metal for the frame and started to cut it to size. I was literally about to start welding when I found a trailer for sale on a local Jeep forum. It was very close to what I planned to build and the price was more than right. I couldn't have bought the materials for what I paid for the trailer.
It was only a little more than an hour away. I drove down thinking I would have to repack the bearings, reconstruct the coupler, etc. but it was in perfect condition. I drove it away and was fully confident with it within 10 miles or so. Thanks Just-lift; good deal!
The overall specs are;
- length 12'
- width 5' 10";
- height 3' 5" (without lid)
- clearance 19.75" to frame
- clearance 15" to axle
- tongue platform tapering to 32"
- weight not sure yet !!!
- axle 3,500 lb. (brakes to come)
- wheels 16" Jeep Moab
- tires 245 75R 16 Goodyear Duratrac
- box length 5'
- box width 4'
- box height 19.25"
- box cubic ft. 32 ft(3)
- tongue jack 1,500 lbs.
Here's what I started with. This pic from the ad for it was either taken on the day it was painted or it was more likely raining. It looked shinier that it was.
The trailer was well constructed. I understand it was used by a welding company to trailer a mobile welder to job sites. The round fenders were well built and nicely tied to the frame with deck plate running boards. It had 14" wheels and tires that were in pretty good shape. I wanted square fenders though and 16" wheels and tires to match my Jeep TJ & XJ so I decided to tear everything off.
I sanded down a pair of 16" Jeep Moab wheels and painted them with Duplicolor wheel paint. I'll eventually get them powder coated. I went with graphite to distinguish them from the silver wheels on the tow vehicles. I found an almost new set of 245/75R/16 Goodyear Duratracs on Kijiji to match what I have on my TJ. I also needed a set of spacers to mount the wheels to the hubs. I may replace the axle so I can add brakes. Unlike a lot of axles the current one does not have the flanges to bolt the brake backing plates to. If I can fabricate something suitable I'll go that route. If not I'll build a new axle.
I cut off the trailer jack that came with the trailer and welded on brackets to attach a 1,500 lb. marine jack. I like the wheel/tire and hope it handles dirt surfaces better than the more common narrow tires.
The trailer bed was pretty rusty and had about 30 bolt, rivet and rust holes that needed to be filled.
Scraps from the old running boards came in handy.
The chassis was built by a company called EZ Tow Trailers. I like the curved side rails which is something I didn't plan for in my original sketches.
I spent a lot of time underneath it getting rid of the rust.
I eventually flipped it over and that seemed like the right time to add a receiver to the rear bumper for a bike rack, etc.
With a lot of the rust gone I painted the frame with POR15 and later with a few different types of cheap aerosol bed liners. I thought I'd try a different ones out and recoat everything with the one I finally like (no decision yet).
Attachments
-
1.9 MB Views: 55
-
1.3 MB Views: 50
-
748.2 KB Views: 46
-
634.4 KB Views: 45
-
1.2 MB Views: 46
Last edited: