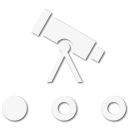
Pioneer I
Well, thought I'd add an update of sorts. Been working on selling our house so that we can move farther north and get out of the city, but the market for our area apparently slowed to a crawl right when I listed it back at the beginning of June. Hopefully we can sell and finish moving before the end of the year, but we'll see.
Since we have to be able to show the house at any given time, I haven't put any work into the Alpha at all. I'm still running without the front drivetrain, haven't touched any of the rear power setup or ARB compressor or anything. Tires are starting to get worn down enough to warrant replacing, but that needs to wait until next spring. And then today the crank position sensor threw a P0335 code again after the engine died on me at a stop light while idling. After replacing the throttle pedal assembly last time I had zero issues, so I'm not sure what it is now since everything is basically brand new in the engine management system as far as sensors go. Might be a connector or something. I might poke around at it this weekend.
I've been holding off doing any work on the Alpha since not only was I quite busy for a while getting half the house moved into a storage unit to get it listed and showable, but I was also hoping to have moved by now and working remotely which would let me start tearing stuff apart on the Alpha without needing to get it all back together in an evening or even a weekend, but no such luck. I might start working on the rear power system again, depending on how much time i have to put into the crankshaft sensor issue. Unfortunately starting next week we are also beginning to move our entire datacenter to a new location, so that's probably going to start chewing into my spare time as well. The fun just never ends.
Since we have to be able to show the house at any given time, I haven't put any work into the Alpha at all. I'm still running without the front drivetrain, haven't touched any of the rear power setup or ARB compressor or anything. Tires are starting to get worn down enough to warrant replacing, but that needs to wait until next spring. And then today the crank position sensor threw a P0335 code again after the engine died on me at a stop light while idling. After replacing the throttle pedal assembly last time I had zero issues, so I'm not sure what it is now since everything is basically brand new in the engine management system as far as sensors go. Might be a connector or something. I might poke around at it this weekend.
I've been holding off doing any work on the Alpha since not only was I quite busy for a while getting half the house moved into a storage unit to get it listed and showable, but I was also hoping to have moved by now and working remotely which would let me start tearing stuff apart on the Alpha without needing to get it all back together in an evening or even a weekend, but no such luck. I might start working on the rear power system again, depending on how much time i have to put into the crankshaft sensor issue. Unfortunately starting next week we are also beginning to move our entire datacenter to a new location, so that's probably going to start chewing into my spare time as well. The fun just never ends.